In the installation of power engineering, cable terminals,
waterproof cable glands and
electrical wire connectors are important components of power equipment in transmission and transformation electricity circuit. Their functions are to distribute the electric field at the shielding cut-off point outside the cable terminals, to protect the cable from breakdown, as well as to insulate and waterproof the cables inside and outside. In cable lines, more than 60% of accidents are caused by accessories, so the quality of connector accessories plays an important role in the safety and reliability of the entire power transmission and transformation.
Cautions in Construction of Common Power Cables
1. Conductor connection
Conductor connection requires low resistance and sufficient mechanical strength, and no sharp angle can appear at the joint. Medium and low voltage cable conductor connection is commonly used by pressure joint, pressure joint should pay attention to:
(1) Select suitable conductivity and mechanical strength of the conductor connection tube;
(2) The matching clearance between the inner diameter of the pressure nozzle and the outer diameter of the connected core is 0.8-1.4 mm.
(3) The resistance of the joints after bonding should not be greater than 1.2 times that of the conductors with equal cross-section, and the tensile strength of the copper conductor joints should not be less than 60N/mm2.
(4) Before pressing, the outer surface of conductor and the inner surface of connecting pipe are coated with conductive adhesive, and the oxide film is destroyed by wire brush.
(5) Connecting pipes, sharp corners on conductors of wire cores, rough edges, etc., polished smooth with a file or sandpaper.
2. Internal semiconductor shielding treatment
Where the cable body has an internal shield layer, it is necessary to restore the internal shield layer in the joint of the conductor part of the pressure nozzle when making the joint. The internal semiconductor shield of the cable should leave a part in order to make the inner shield of the joint on the connecting tube interconnect with each other and ensure the continuity of the internal semiconductor, so as to make the field strength at the joint joint pipe uniformly distribute.
3. Treatment of external semiconductor shielding
External semiconductor shielding is a semi-conductive material which acts as a uniform electric field outside the insulation of cables and joints. Like internal semiconductor shielding, it plays a very important role in cables and joints. The external semiconductor ports must be neat and uniform, and smooth transition with insulation is required. The winding of the semiconductor band at the junction is overlapped and connected with the external semiconductor shielding of the cable body.
4. Treatment of Cable Reaction Cone
During construction, the shape and accuracy of the reaction cone are equal in the potential distribution on the whole cone surface. When making the reaction cone of cross-linked cable, special cutting tools are usually used, and slightly heated by a slight fire, cutting with a fast knife. After basic shaping, the reaction cone is repaired and scraped with 2 mm thick glass. Finally, sandpaper is polished from coarse to fine until smooth.
5. Metal shielding and grounding treatment
Metal shielding is mainly used to conduct short-circuit current of cable faults and electromagnetic interference of shielding electromagnetic field to nearby communication equipment. Metal shielding is in zero potential under good grounding state in operation state. When cable faults occur, it has the ability to transmit short-circuit current in a very short time. The grounding wire should be welded reliably. The metal shield and armor band on the body of the box cables at both ends should be welded firmly. The grounding of the terminal should be reliable.
Electrical wire connector
6. Sealing and Mechanical Protection of connectors
Sealing and mechanical protection of connectors are the guarantee to ensure the safe and reliable operation of connectors. Water and moisture should be prevented from infiltrating into the connectors. In addition, connector protection grooves or cement protection boxes should be built at the joint location.
Cautions in Construction of Common Power Cables
1. When installing cables and thermal pipes in parallel, the distance between cables and thermal pipes should be 2 m, and 0.5 m when crossing.
2. When installing cables parallel to or cross with other pipelines, the distance between cables and other pipelines should be kept at 0.5m.
3. When the cable is directly buried, the buried depth of 1-35kV cable should not be less than 0.7m.
The net distance between cable 4, 10 kV and below is not less than 0.1 M when installed in parallel, 10-35 kV is not less than 0.25 m when installed in parallel and 0.5 m when crossed.
5. The minimum bending radius of the cable shall not be less than 15D for multi-core cable and 20D for single-core cable (D is the outer diameter of the cable).
6, 6 kV and above cable joints
a. When installing the cable terminal, the semi-conductive shielding layer must be stripped, the insulation must not be damaged during operation, the knife marks and bumps should be avoided, and sandpaper should be used when necessary. The shielding end should be flat and the graphite layer (carbon particles) should be cleaned up.
b. Copper shielding and steel armor at the end of plastic insulated cable must be grounded well, and this principle should be followed for short lines to avoid induction electromotive force at the end of steel armor, or even "fire" and combustion sheath accidents when three-phase unbalanced operation occurs. Tin-plated braided copper and cable copper strip should be used to connect the grounding lead wire, and soldering with soldering iron and tin should not be used to seal the grounding lead wire, so as to avoid burning insulation.
c. And three-phase copper shielding should be connected with the ground wire separately. Attention should be paid to the shielding ground wire and steel armoured ground wire should be drawn out separately and insulated from each other. The position of welding ground wire should be as far as possible.
7. Basic requirements for cable terminals and intermediate terminals:
a. Conductors are well connected.
B. The insulation is reliable. It is recommended to use radiation crosslinking thermal shrinkage silicone rubber insulation material.
c. Good sealing;
d. Sufficient mechanical strength to adapt to various operating conditions.
8. The end of the cable must be waterproof and corrosive to prevent breakdown due to aging of insulation caused by water trees.
9. Cranes and forklifts must be used in the handling of cables. It is forbidden to transport and lay them flat. Cable laying trucks should be used in the installation of large cables to avoid damage of cables caused by external forces or abrasion of sheaths and insulating layers caused by manual dragging. Cables are not mounted on discs. Manpower is strictly prohibited to pull them by hand, so that conductors bend and damage the insulating layer, resulting in short circuit.
10. If the cable cannot be laid in time for some reasons, it should be stored in a dry place to prevent sunlight exposure and water intake at the end of the cable.
This article is arranged by cable joints. This article does not represent the viewpoint of our site.
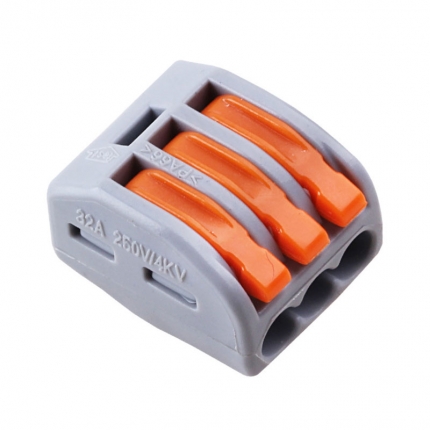